What is Lean Methodology?
Lean methodology is a business management approach focused on reducing waste while creating value for the customer. Rooted in principles of efficiency, Lean’s goal is to eliminate non-value-adding processes, speed up operations, and improve customer satisfaction. When applied in lean manufacturing, it ensures that every step in production is purposeful, cost-effective, and aligned with customer needs.
Key Goals of Lean Methodology:
- Reduce Waste: Identify and remove unnecessary steps that don’t add value.
- Optimize Operations: Streamline workflows to maximize efficiency and speed.
- Increase Customer Satisfaction: Deliver exactly what customers need, when they need it.
Lean methodology is applicable across various sectors, from manufacturing to service industries. With the integration of digital transformation tools, Lean becomes even more powerful, enabling real-time insights, predictive maintenance, and a highly responsive production environment. Further Reading
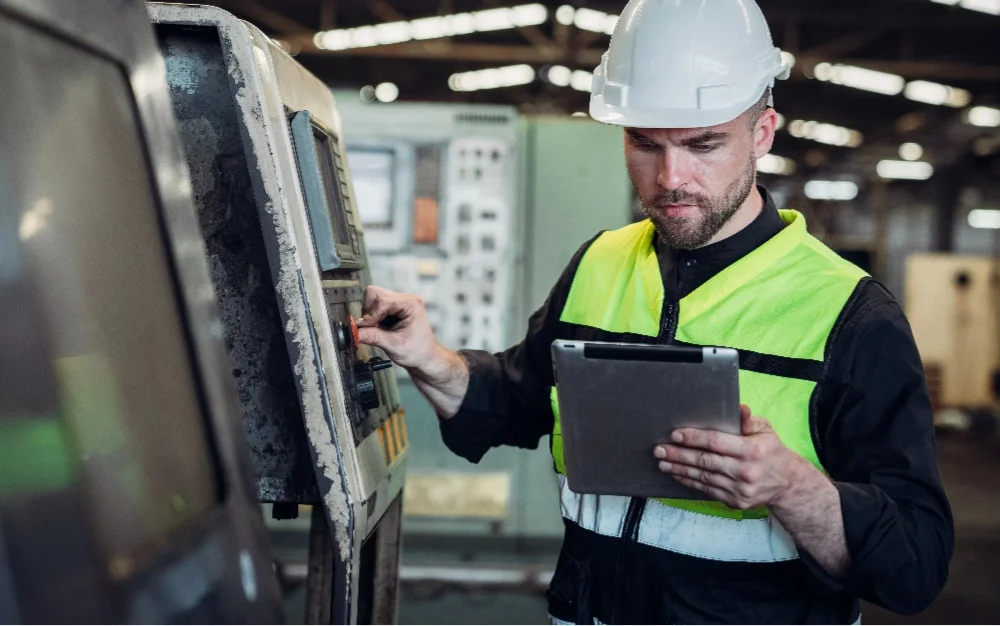
What is Lean Manufacturing?
Lean manufacturing is a transformative strategy designed to streamline production, reduce lead times, and enhance responsiveness to both customers and suppliers. By focusing on eliminating waste and optimizing every step of the process, Lean manufacturing tackles daily challenges on the factory floor, converting potential bottlenecks into opportunities for improvement.
Why Lean Manufacturing is Key for Digital Excellence:
- Boost Production Speed: Lean manufacturing significantly reduces production times, enabling teams to meet demanding KPIs for efficiency and on-time delivery.
- Enhance Responsiveness: By removing waste, Lean helps manufacturing teams react faster to customer needs and supplier demands, elevating agility and satisfaction.
- Eliminate Inefficiencies: Lean identifies and eliminates non-value-adding activities, transforming operations into a highly efficient, cost-effective process.
- Achieve a Competitive Edge: With a commitment to continuous improvement, Lean manufacturing ensures peak performance, keeping you ahead of the competition in quality and speed.
In today’s digital era, integrating Lean with digital transformation tools—such as real-time data monitoring, predictive analytics, and AI-driven improvements—supercharges these benefits. Lean manufacturing is more than a process; it’s a pathway to achieving industry-leading performance and driving impactful results across all areas of digital excellence.
Key Elements of Lean Manufacturing
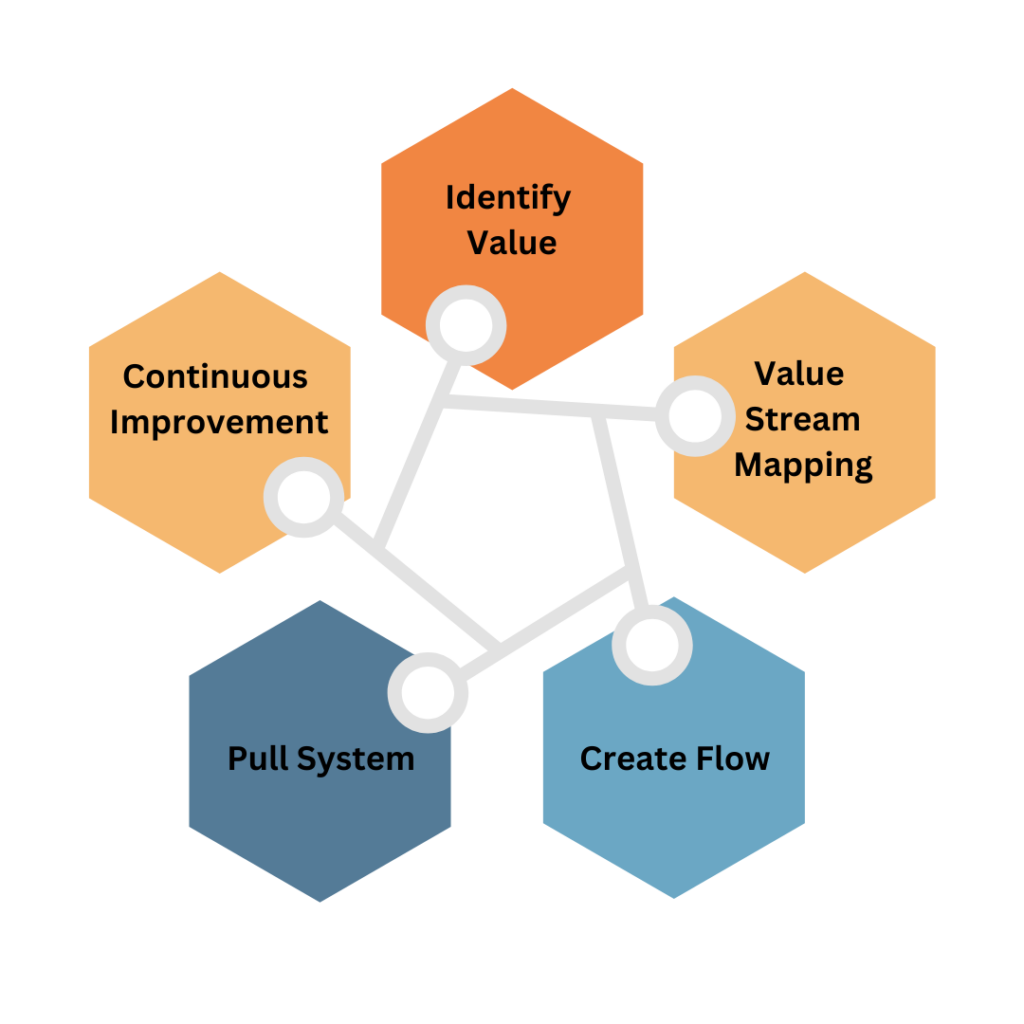
1. Customer-Centric Value Creation:
Imagine a factory that manufactures custom car parts. By collecting real-time data on customer orders, preferences, and quality feedback, the production line adapts quickly to meet these unique demands.
As George Westerman from MIT Sloan said, “Digital transformation is not about technology but how you shape it to serve your customers better.” Further Reading
With digital tools, the manufacturing team gains insights directly from the customer, ensuring every product matches the client’s exact needs. This customer-focused approach is the foundation of Lean.
2. Value Stream Mapping:
Consider a production line for electronics where complex steps can cause bottlenecks. By using advanced data analytics and digital mapping tools, teams can visualize every phase, quickly identifying where delays or excess resource use occurs.
As W. Edwards Deming said, “Without data, you’re just another person with an opinion.” Further Reading Data-driven mapping transforms each step into actionable insights, allowing teams to pinpoint inefficiencies and make precise improvements.
The Impact of Data-Driven Mapping:
- Identify and Eliminate Bottlenecks: Real-time digital mapping helps teams spot and address bottlenecks instantly, improving workflow and meeting efficiency KPIs.
- Optimize Resource Allocation: By monitoring resource usage at every stage, data-driven mapping enables targeted adjustments that reduce waste and enhance productivity.
- Foster Continuous Improvement: With actionable insights, teams can make informed decisions to continuously improve processes, ensuring every phase operates at peak efficiency.
Digital transformation elevates data-driven mapping, making Lean manufacturing more effective by aligning every step with performance and efficiency goals.
3. Ensuring Continuous Flow:
In lean manufacturing, achieving a seamless, continuous flow is crucial for maximizing productivity and minimizing downtime. Picture a textile factory where IoT sensors continuously monitor machine performance in real-time. Instead of waiting for breakdowns that halt production, these sensors proactively alert maintenance teams to potential issues before they become disruptive. This predictive maintenance, driven by digital transformation, ensures that every piece of equipment runs efficiently, keeping the production line in constant motion.
The Power of Digital Transformation for Continuous Flow:
- Real-Time Bottleneck Detection: Digital tools provide instant insights, allowing teams to identify and resolve bottlenecks immediately, helping meet critical KPIs for productivity.
- Prevent Unexpected Downtime: Predictive data enables proactive maintenance, reducing costly downtime and ensuring operations stay on track.
- Optimize Production Efficiency: By sustaining continuous flow, digital transformation drives a steady, reliable output, ensuring high levels of performance and responsiveness to demand.
This approach transforms continuous flow from a goal into a sustainable reality, helping digital leaders in manufacturing achieve seamless operations, efficient resource use, and an edge in productivity.
4. Pull System:
Incorporating a demand-driven, or pull system, aligns manufacturing output with real customer demand, reducing waste and optimizing efficiency. For example, a furniture manufacturer relying on forecasts may build up excess inventory and storage costs. A pull system initiates production only when orders are confirmed, ensuring resources are effectively used and products delivered just-in-time.
Digital tools amplify this approach by integrating CRM systems with real-time analytics, allowing teams to quickly respond to customer needs. As Satya Nadella of Microsoft puts it, “Our goal is to empower the team to own the customer outcome.” (McKinsey & Company)Leveraging these technologies ensures production is precisely aligned with customer expectations, enhancing both efficiency and satisfaction.
5. Perfection and Continuous Improvement (Kaizen):
Kaizen, or continuous improvement, is a core principle in Lean manufacturing, focusing on making small, consistent changes that drive significant improvements over time. This approach builds a culture of ongoing enhancement, where each incremental adjustment contributes to long-term success.
As Japanese industrialist Masaaki Imai, often called the “Father of Kaizen,” explained, “Kaizen is everyday improvement, everybody improvement, everywhere improvement.” Digital transformation elevates Kaizen by tracking and analyzing each change, giving teams the data they need to measure progress and align improvements with key performance indicators (KPIs).
Why Digital Tools Amplify Kaizen:
- Track Incremental Changes: Digital tools document each improvement, enabling teams to see progress over time and make adjustments based on real data.
- Achieve Measurable Outcomes: By quantifying the impact of small changes, teams can directly measure improvements in productivity, quality, and efficiency.
- Foster a Culture of Continuous Growth: Digital support makes it easier for all team members to engage in continuous improvement, building a collective commitment to excellence.
Integrating Kaizen with digital tools makes Lean manufacturing more effective, helping teams maintain steady progress toward operational excellence and ensuring that every improvement is measurable and impactful. Further Reading
Lean methodology is not only applicable to large-scale production lines but also brings high efficiency to small and medium-sized manufacturers. Minimizing waste on the production floor and producing the right product at the right time impacts customer satisfaction and elevates the overall performance of your business.
4 Essential Steps for Applying Lean Methodology in the Manufacturing Industry
5S Implementation: Building Organization and Cleanliness
The 5S system is a core practice in Lean manufacturing, designed to create an organized, efficient, and clutter-free workplace. Originating in Japan and widely adopted worldwide, 5S transforms factory floors and office spaces alike by focusing on five essential steps:
- Seiri (Sort): Remove unnecessary items to eliminate clutter and create a focused workspace.
- Seiton (Set in Order): Arrange tools and materials for easy access, reducing the time spent searching.
- Seiso (Shine): Clean and maintain the workspace regularly for safety and efficiency.
- Seiketsu (Standardize): Establish and maintain organization and cleanliness standards across all teams.
- Shitsuke (Sustain): Foster discipline to consistently uphold these standards, embedding them into the workplace culture.
The 5S methodology is applied globally, from Toyota’s assembly lines to tech companies’ offices, enhancing productivity and supporting a safer, more organized work environment. By reducing waste and maintaining order, 5S empowers employees to work more effectively and with fewer disruptions. Further Reading
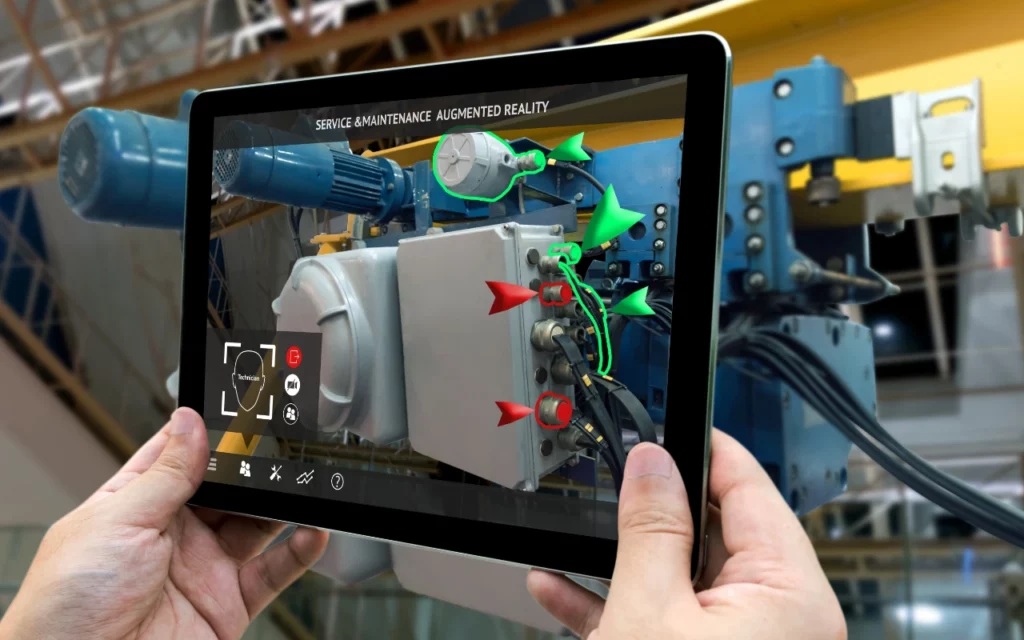
Just-in-Time (JIT) Production: On-Demand Efficiency
Just-in-Time (JIT) production is a Lean manufacturing strategy that ensures items are produced only when needed, minimizing stockpiling and excess inventory costs. This approach:
- Minimizes storage costs by producing only as required,
- Prevents overproduction by aligning output with actual demand,
- Enables faster response to customer orders, meeting demand without delay.
JIT was key to Toyota’s success and is now used in industries from automotive to electronics. For example, an auto manufacturer using JIT orders parts only when a customer places an order, ensuring resources are efficiently utilized. Through digital transformation tools like real-time demand tracking, JIT’s impact is magnified, aligning production precisely with market needs and eliminating delays across the entire process. Further Reading
Kaizen: Driving Continuous Improvement
Kaizen, meaning “continuous improvement” in Japanese, promotes incremental, ongoing changes that lead to significant advancements over time. In Lean manufacturing, Kaizen fosters a culture where everyone—frontline workers and management alike—contributes to daily improvements.
- Encourages small, regular adjustments that compound into substantial improvements,
- Empowers employees to make suggestions and implement changes, and
- Tracks improvements with digital tools, allowing teams to see direct impacts on productivity and quality.
Companies like Toyota, Honda, and Amazon embed Kaizen into their culture, where employees regularly contribute ideas and solutions. This consistent approach to improvement enables organizations to stay adaptable, resilient, and efficient in today’s competitive market.
Poka-Yoke: Ensuring Error-Free Quality
Poka-Yoke, or “mistake-proofing,” is a Lean method designed to prevent errors before they occur. Originally developed at Toyota, Poka-Yoke ensures workers complete tasks correctly every time, reducing errors and safeguarding quality. For example:
- Assembly fixtures may be designed so parts only fit one way, eliminating assembly errors.
- Sensors in electronics manufacturing ensure each component is correctly positioned before assembly continues, preventing potential missteps.
Today, Poka-Yoke is widely used across industries to guarantee quality. When combined with digital tools, Poka-Yoke is even more effective, providing real-time alerts so teams can detect and correct issues immediately. This technology saves time, preserves quality, and ensures error-free production.
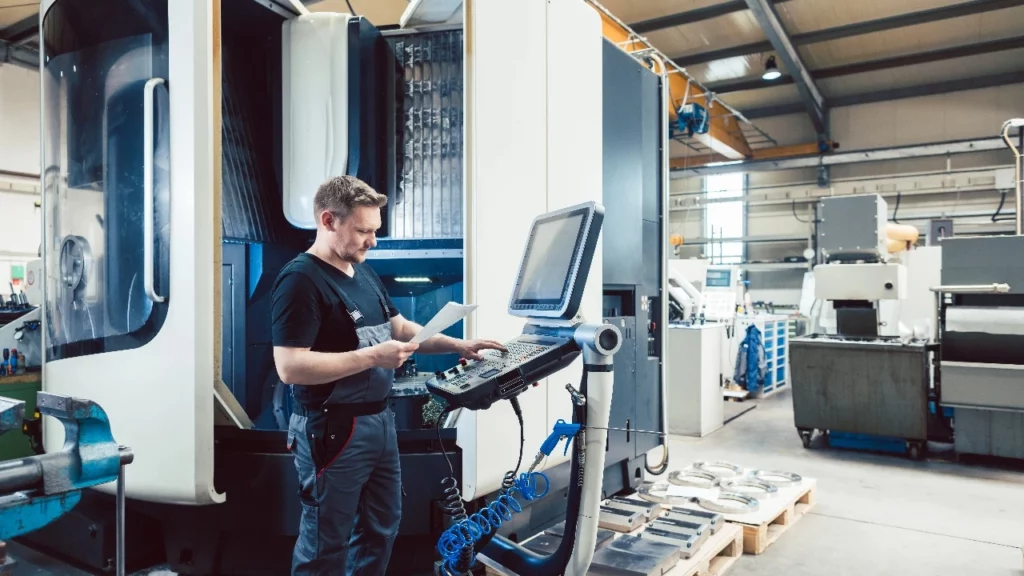
VSight’s Role: Strengthening Lean Through Digital Transformation
In modern manufacturing, digital transformation has amplified the effectiveness of Lean principles. VSight enhances Lean practices by integrating augmented reality (AR) remote assistance and artificial intelligence (AI) solutions on the production floor, making daily operations more efficient and streamlined. These tools empower manufacturing teams to overcome challenges quickly and maintain smooth operations.
AR Remote Assistance for Connected Workers
VSight’s AR Remote Assistance empowers connected workers by enabling real-time collaboration between experts and on-site personnel, regardless of location. This feature allows rapid resolution of technical issues and breakdowns, reducing downtime and keeping production running smoothly. With this connected worker technology, manufacturing teams can ensure continuous operations without extended interruptions.
Digital Work Instructions and Standard Operating Procedures (SOPs)
The VSight Connected Worker Platform simplifies complex tasks and maintenance processes through digital work instructions and SOPs. Digital step-by-step guidance enables workers to follow standardized processes accurately, minimizing errors and enhancing productivity. This feature also supports standard work instructions and procedures, ensuring that every task is performed consistently across the organization.
VSight VideoFlow for AI-Powered Knowledge Capture and Training
VSight VideoFlow uses AI to transform recorded videos into structured work instructions, training materials, and onboarding content. This AI-driven process streamlines knowledge capture, ensuring that expertise is easily documented and shared across teams. By automating the creation of standardized procedures, VideoFlow simplifies training and boosts consistency, providing employees with accessible digital resources for continuous learning and improvement.
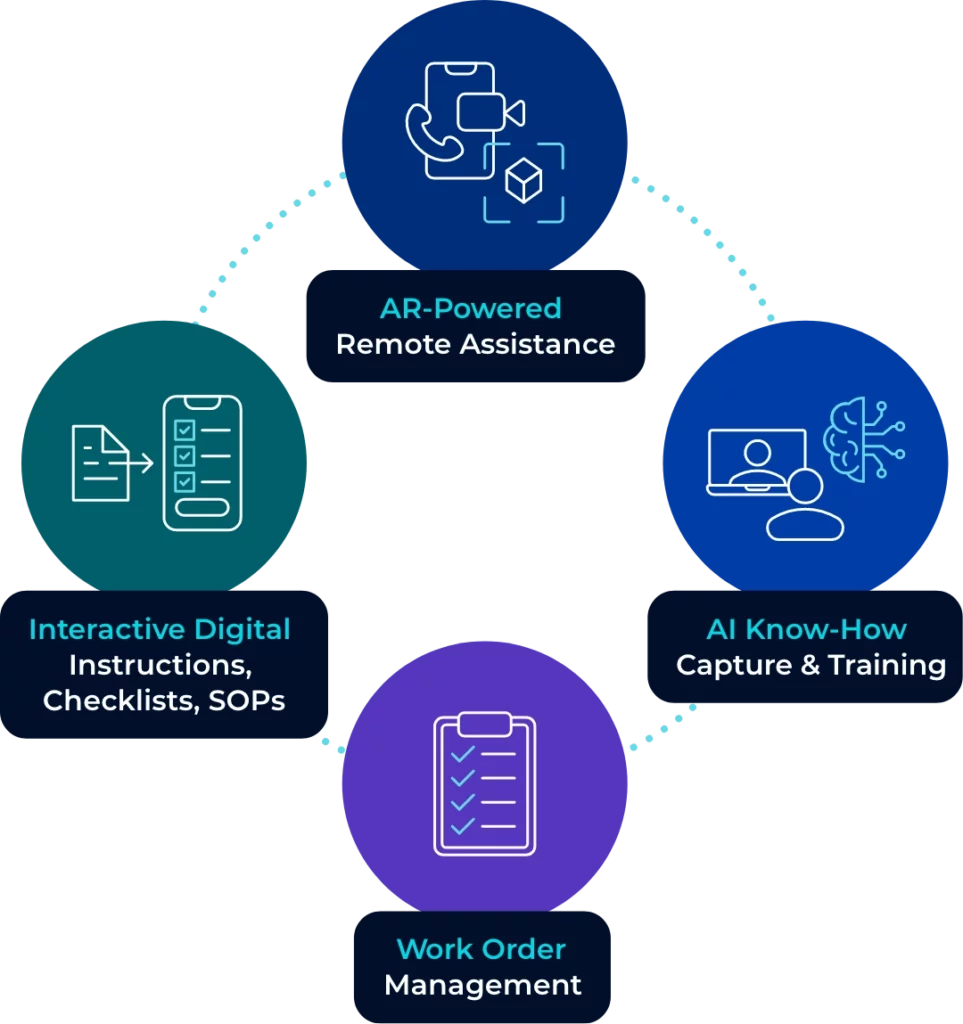
Discover the VSight Connected Worker Platform—your partner in Lean manufacturing excellence
As a manufacturing excellence leader, you know that Lean methodology is key to reducing waste, maximizing efficiency, and controlling costs. With VSight, you can unlock the full potential of Lean principles by integrating advanced digital tools directly into your production floor.
Discover how VSight optimizes your production processes for sustainable growth and competitive advantage. Book a Demo today and experience the future of Lean with VSight!