What is Uptime and Downtime in Industrial Operations?
In the dynamic landscape of industrial operations, two key terms play a pivotal role in determining efficiency, productivity, and profitability: uptime and downtime. Whether in the realm of machinery manufacturing, oil & gas exploration, mining operations, automotive assembly lines, or other industries, grasping the significance of these concepts is essential for optimizing performance and ensuring smooth operations.
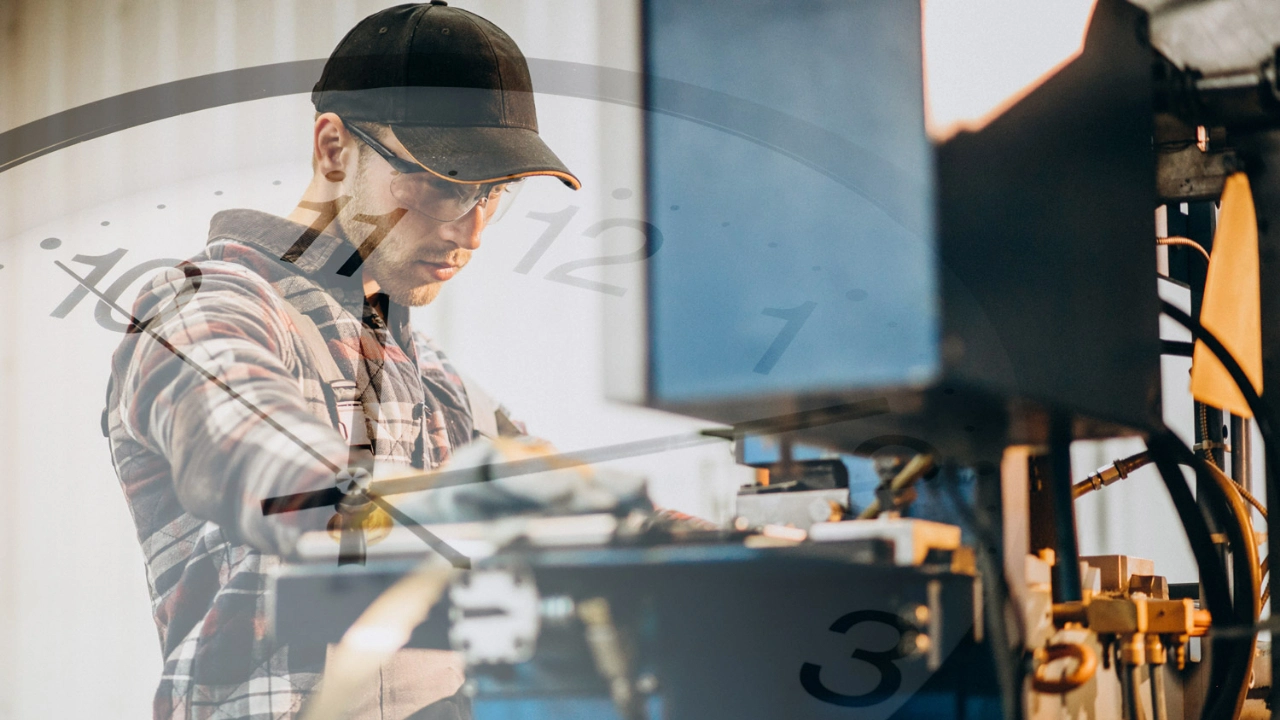
In the dynamic landscape of industrial operations, two key terms play a pivotal role in determining efficiency, productivity, and profitability: uptime and downtime. Whether in the realm of machinery manufacturing, oil & gas exploration, mining operations, automotive assembly lines, or other industries, grasping the significance of these concepts is essential for optimizing performance and ensuring smooth operations.
Uptime: Keeping the Wheels Turning
Uptime is the heartbeat of industrial operations. It represents the duration during which systems, equipment, or machinery are operational and available for use. Think of it as the green light signaling that production processes are in full swing, services are being rendered, and functions are performing as intended.
In industries where every minute counts, such as machinery manufacturing, uptime is the lifeline that keeps production lines humming. It ensures that critical equipment, from CNC machines to assembly robots, remains operational, enabling seamless production and timely delivery of goods.
Likewise, in sectors like oil & gas exploration and mining, uptime is synonymous with continuous operations. It means drilling rigs are extracting oil, gas wells are flowing, and mining equipment is digging up valuable minerals without interruption. Maximizing uptime in these industries is paramount for meeting production targets, optimizing resource utilization, and driving profitability.
Downtime: When the Machinery Stands Still
On the flip side, downtime represents the period when systems, equipment, or machinery are non-operational or unavailable for use. It’s the red flag signaling that something has disrupted the smooth flow of operations, whether it’s an unexpected breakdown, scheduled maintenance, or other planned or unplanned events.
In the fast-paced world of industrial operations, downtime is akin to hitting the pause button on productivity. It leads to production delays, idle equipment, and lost opportunities, all of which can have a significant impact on the bottom line.
For example, in automotive assembly lines, even a brief downtime event can disrupt the entire production schedule, leading to bottlenecks and cascading delays down the line. Similarly, in mining operations, downtime due to equipment failures or maintenance can result in lost production time and revenue.
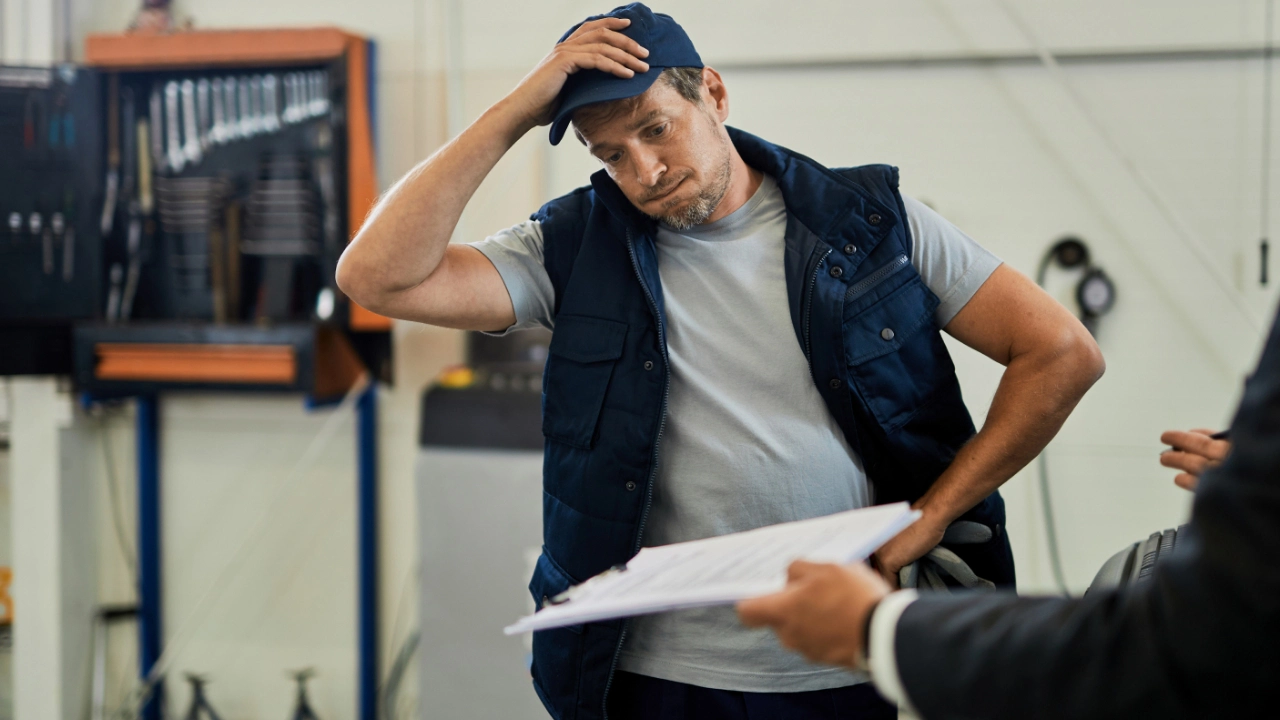
Strategies for Success: Minimizing Downtime, Maximizing Uptime
Given the critical role of uptime and the detrimental effects of downtime, industries implement various strategies to optimize performance and operational efficiency.
Proactive Maintenance:
Implementing preventive maintenance programs to identify and address potential issues before they escalate into downtime events.
Real-time Monitoring:
Leveraging advanced monitoring technologies, such as IoT sensors and predictive analytics, to detect anomalies and anticipate equipment failures.
Efficient Troubleshooting:
Equipping maintenance teams with the tools and expertise needed to quickly diagnose and resolve issues, minimizing downtime and maximizing uptime.
Scheduled Downtime:
Planning and scheduling maintenance activities during planned downtime windows to minimize disruptions to production schedules.
Continuous Improvement:
Embracing a culture of continuous improvement to streamline processes, optimize workflows, and reduce downtime-related losses over time.
In today’s increasingly interconnected world, leveraging technology can offer new avenues for optimizing uptime and minimizing downtime. Augmented Reality (AR) platforms and digital step-by-step work instructions in the form of workflows can be valuable tools for remote collaboration and troubleshooting.
AR platforms allow maintenance technicians and operators to access real-time information, overlays, and instructions directly within their field of view, enhancing their ability to perform tasks accurately and efficiently. Similarly, digital workflows provide detailed, step-by-step guidance for complex procedures, ensuring consistency and reducing the risk of errors, even when teams are geographically dispersed.
By integrating AR platforms and digital workflows into their operations, industrial organizations can empower their teams to collaborate effectively across distances, streamline maintenance and troubleshooting processes, and ultimately maximize uptime while minimizing downtime-related disruptions.
By understanding the factors that influence uptime and downtime and implementing strategies to maximize uptime and minimize downtime aligned with an optimized expert utilization rate, industrial operators can keep their operations running smoothly, meet production targets, and stay ahead in today’s competitive landscape. With the emerging technologies such as AR platforms, it is possible to unlock new possibilities for remote collaboration and efficiency, ensuring that operations remain on track, no matter the circumstances.
Learn more about VSight
See how VSight can help you with your field service, maintenance, onboarding and training operations.