What is Lean Manufacturing?
Lean Manufacturing is a systematic approach to minimizing waste without compromising productivity in manufacturing processes. Originating from the Toyota Production System (TPS) in the 1940s, Lean Manufacturing has since been adopted globally across various industries. The methodology focuses on maximizing value for the customer while eliminating waste, leading to improved efficiency, reduced costs, and enhanced quality. The approach is based on the principle of continuous improvement and involves everyone in the organization, from top management to frontline workers, in the pursuit of operational excellence.
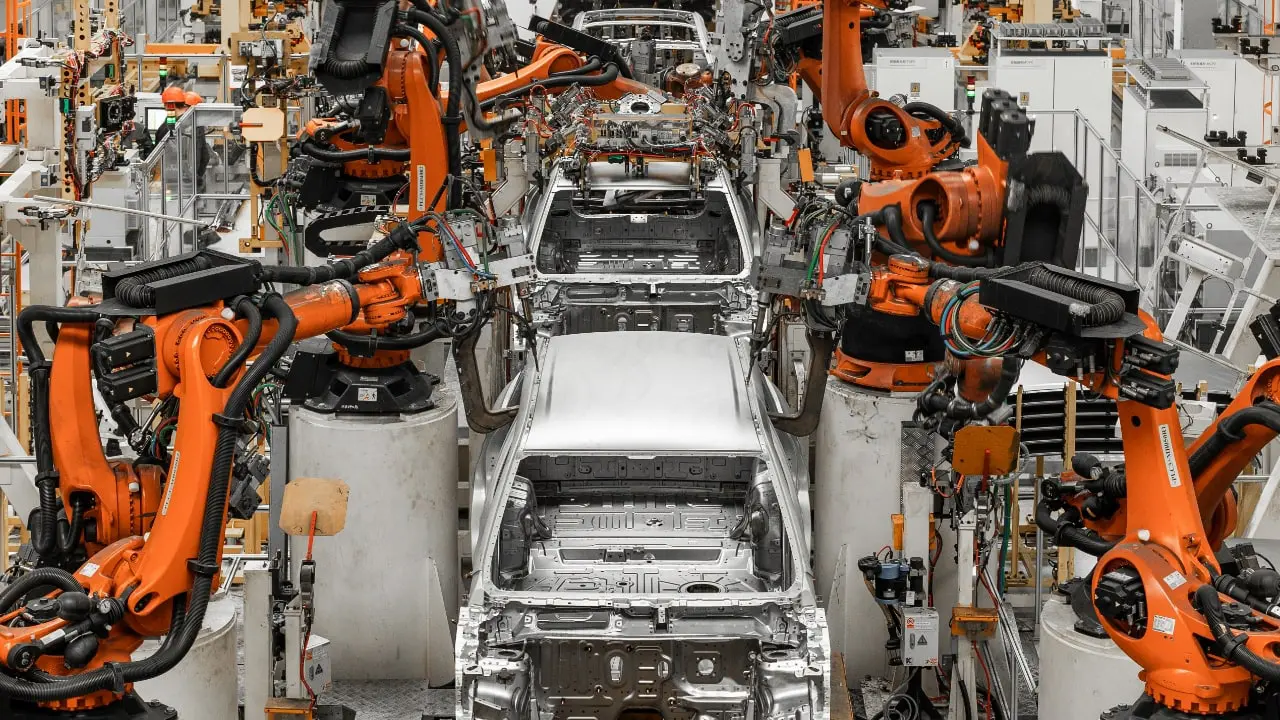
Key Principles of Lean Manufacturing
Value
The first principle of Lean Manufacturing is to define value from the customer’s perspective. This involves identifying what the customer is willing to pay for and focusing all efforts on delivering that value.
Value Stream
The value stream refers to the entire process required to deliver a product or service to the customer. Lean Manufacturing involves mapping out the value stream to identify and eliminate waste in each step of the process.
Flow
Once waste has been identified and removed, the next step is to ensure that the production process flows smoothly without interruptions or bottlenecks. This involves optimizing the layout of the production line, balancing workloads, and improving coordination between different stages of production.
Pull
Lean Manufacturing adopts a pull-based production system, where production is driven by actual customer demand rather than forecasts. This reduces overproduction, minimizes inventory, and ensures that resources are used efficiently.
Perfection
The final principle of Lean Manufacturing is the pursuit of perfection through continuous improvement. This involves regularly reviewing and refining processes to eliminate waste, reduce variability, and enhance quality.
Types of Waste in Lean Manufacturing
Lean Manufacturing identifies seven types of waste, commonly known by the acronym TIMWOOD:
Transportation
Unnecessary movement of materials or products.
Inventory
Excess stock that is not needed immediately.
Motion
technologies enable predictive maintenance by monitoring equipment conditions in real time and forecasting potential failures. This proactive approach allows industries to address issues before they lead to downtime, optimizing MTTF and reducing the frequency of repairs.
Waiting
Idle time when resources are not being used effectively.
Overproduction
Producing more than is needed or before it is needed.
Overprocessing
Performing more work or using more resources than necessary.
Defects
Producing defective products that require rework or are discarded.
Benefits of Lean Manufacturing
Reduced Waste
Lean Manufacturing helps organizations identify and eliminate waste, leading to more efficient use of resources and lower production costs.
Improved Quality
By focusing on value and continuous improvement, Lean Manufacturing enhances product quality and reduces defects.
Faster Time-to-Market
Lean principles streamline production processes, allowing organizations to respond quickly to customer demand and bring products to market faster.
Increased Flexibility
Lean Manufacturing enables organizations to adapt quickly to changes in customer demand, market conditions, or production requirements.
Enhanced Employee Engagement
Lean Manufacturing fosters a culture of continuous improvement, where employees at all levels are encouraged to contribute ideas and take ownership of their work.
Lean Manufacturing in Industrial Use-Cases
Lean Manufacturing principles have been successfully applied across various industries, demonstrating their versatility and effectiveness in improving operational efficiency, reducing waste, and enhancing product quality. Here are some notable examples of Lean Manufacturing in action across different sectors:
Automotive
The automotive industry, particularly Toyota, is the birthplace of Lean Manufacturing. The Toyota Production System (TPS) is the foundation of Lean practices. Automotive companies worldwide have adopted Lean to streamline their production lines, reduce lead times, and improve vehicle quality. For example, Ford Motor Company implemented Lean principles to eliminate bottlenecks in its assembly process, significantly reducing the time required to build a vehicle while maintaining high standards of quality.
Aerospace
In aerospace, precision and safety are paramount. Companies like Boeing and Airbus use Lean Manufacturing to reduce production waste, improve workflow, and ensure the highest quality standards. Lean has enabled these companies to optimize their supply chains, reduce inventory costs, and improve the on-time delivery of aircraft. The focus on continuous improvement has also driven innovations in manufacturing processes, such as the adoption of advanced materials and automation technologies.
Electronics
The electronics industry faces rapid technological advancements and high customer demand for innovative products. Lean Manufacturing helps electronics companies like Samsung to respond quickly to market changes by minimizing waste and reducing the time-to-market for new products. By adopting Lean principles, these companies have improved their production flexibility, reduced the risk of overproduction, and enhanced their ability to meet customer demand with just-in-time manufacturing.
Healthcare
Lean Manufacturing has found applications in the healthcare sector, where it is used to improve patient care, reduce waiting times, and optimize the use of resources. Hospitals and healthcare providers have applied Lean principles to streamline processes, such as patient admissions, surgery scheduling, and inventory management.
Food and Beverages
The food and beverage industry benefits from Lean Manufacturing by optimizing production processes, reducing waste, and ensuring product quality. Companies like Nestlé and Coca-Cola use Lean to enhance their manufacturing efficiency, reduce energy consumption, and minimize the environmental impact of their operations. Lean principles also help these companies maintain consistent product quality by standardizing processes and reducing variability in production.
Construction
Lean Manufacturing principles are increasingly being applied in the construction industry to improve project management, reduce waste, and enhance efficiency. Construction companies use Lean to optimize workflows, improve coordination between teams, and ensure that projects are completed on time and within budget. For example, Lean practices have been used in the construction of hospitals, schools, and commercial buildings to reduce material waste, improve safety, and enhance the overall quality of construction projects.
Oil and Gas
The oil and gas industry utilizes Lean Manufacturing to optimize production processes, reduce downtime, and improve safety. Companies like Shell and BP have implemented Lean practices to enhance the efficiency of their operations, reduce the time required for maintenance activities, and minimize the environmental impact of their operations. Lean principles have also been applied to improve supply chain management and reduce the cost of exploration and production activities in the oil and gas sector.
Lean Manufacturing and Connected Worker Platforms
Lean Manufacturing principles can be effectively implemented and sustained using Connected Worker Platforms. These digital solutions provide real-time visibility into production processes, enable seamless communication across teams, and facilitate data-driven decision-making. By integrating Connected Worker Platforms with Lean Manufacturing practices, organizations can further reduce waste, optimize processes, and achieve operational excellence.
Lean Manufacturing is a powerful methodology for improving efficiency, reducing costs, and enhancing quality in industrial operations. By focusing on value, eliminating waste, and continuously improving processes, organizations can achieve significant competitive advantages. The integration of Connected Worker Platforms with Lean Manufacturing practices offers additional benefits, enabling organizations to leverage digital tools to drive continuous improvement and operational excellence. As industries continue to evolve, Lean Manufacturing remains a vital strategy for achieving sustainable success in a highly competitive market.
Learn more about VSight
See how VSight can help you with your field service, maintenance, onboarding and training operations.