What is 6 Sigma?
6 Sigma is a data-driven methodology and set of techniques for eliminating defects in any process, aiming for near perfection. 6 Sigma uses statistical tools to identify and remove causes of errors and variability, ensuring consistent quality and efficiency. The goal of 6 Sigma is to achieve a process that produces no more than 3.4 defects per million opportunities.
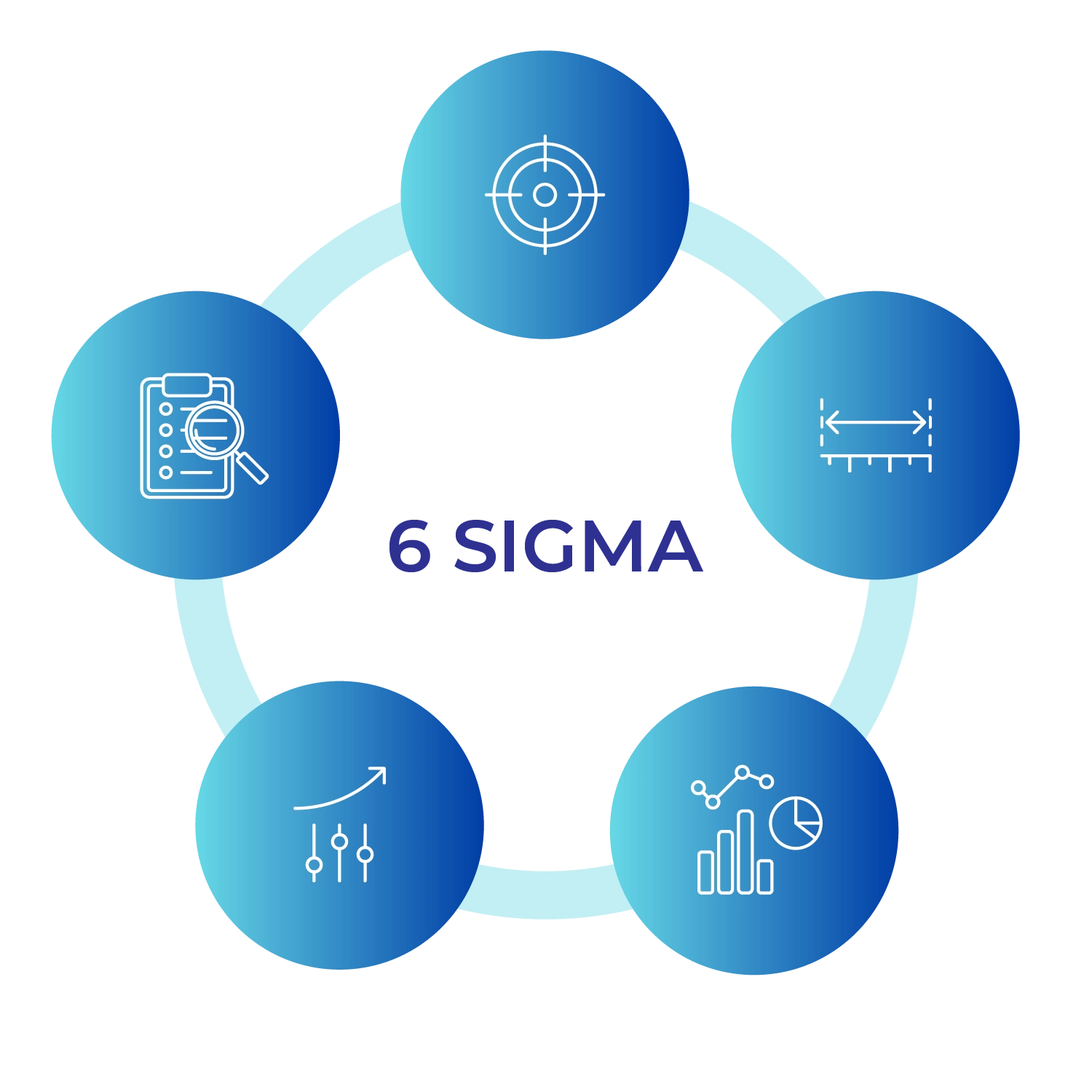
Types of 6 Sigma
DMAIC (Define, Measure, Analyze, Improve, Control):
A data-driven improvement cycle used for optimizing and stabilizing existing processes. Each phase serves a specific purpose:
Define: Identify the problem and project goals.
Measure: Collect data and establish baselines.
Analyze: Identify root causes of defects.
Improve: Implement solutions to eliminate defects.
Control: Maintain improvements and monitor the process.
DMADV (Define, Measure, Analyze, Design, Verify):
Used for creating new product or process designs:
Define: Define project goals and customer deliverables.
Measure: Measure and determine customer needs and specifications.
Analyze: Analyze process options to meet customer needs.
Design: Design the process or product.
Verify: Verify the design performance and ability to meet customer needs.
6 Sigma Principles
6 Sigma is built upon a foundation of key principles designed to improve processes and eliminate defects. These principles guide the methodology and provide a framework for achieving significant operational improvements:
Customer Focus:
The primary goal of 6 Sigma is to meet and exceed customer expectations. Understanding customer needs and requirements is crucial for any 6 Sigma project. This principle ensures that any process improvements directly enhance customer satisfaction.
Data-Driven Decision Making:
6 Sigma relies heavily on data and statistical analysis to identify problems, measure performance, and evaluate solutions. Decisions are based on empirical evidence rather than assumptions or intuition.
Process Focus:
6 Sigma views business processes as the root cause of most issues. By focusing on process improvement, organizations can achieve more consistent and predictable outcomes. This principle emphasizes the importance of process mapping, analysis, and redesign.
Proactive Management:
Rather than reacting to problems after they occur, 6 Sigma encourages proactive management practices. This involves anticipating issues, preventing defects, and continuously monitoring processes to ensure they remain within acceptable limits.
Collaboration and Teamwork:
Effective implementation of 6 Sigma requires collaboration across various functions and departments. Teamwork ensures that different perspectives are considered, and collective expertise is utilized to solve complex problems.
Continuous Improvement:
6 Sigma is an ongoing journey rather than a one-time initiative. Continuous improvement is ingrained in the methodology, promoting a culture where regular assessments and enhancements are part of the organizational routine.
Accountability and Ownership:
6 Sigma assigns clear roles and responsibilities to team members. Everyone involved in a 6 Sigma project is accountable for specific tasks and outcomes, ensuring that there is ownership and commitment to achieving the desired results.
Examples of 6 Sigma
After-Sales Services:
6 Sigma principles ensure consistent quality in after-sales services, reducing errors and enhancing customer satisfaction through continuous improvement. For instance, by applying 6 Sigma to service processes, companies can reduce the number of service calls, improve response times, and enhance the overall customer experience.
Periodic Maintenance Dynamics:
6 Sigma methodologies are applied to improve the efficiency and effectiveness of periodic maintenance schedules. This minimizes downtime and extends equipment life by systematically identifying and eliminating the root causes of maintenance issues, thereby ensuring that maintenance activities are performed optimally and cost-effectively.
Onboarding:
Streamlining onboarding processes to reduce errors and improve employee training. For example, 6 Sigma can help identify and eliminate bottlenecks in the onboarding process, ensuring new employees are productive faster.
Training:
Providing structured training programs to ensure employees are well-versed in 6 Sigma principles. This includes developing training materials and courses that align with 6 Sigma methodologies to ensure consistent quality and performance.
Integrated Logistics Support:
Enhancing logistics support through process improvement and defect reduction. 6 Sigma helps in identifying inefficiencies in the supply chain and implementing solutions to improve logistics operations.
Auditing and Inspecting:
Applying statistical tools to audit and inspect processes, ensuring compliance with quality standards. This can involve regular quality audits and inspections to ensure processes are followed correctly and standards are met.
Industry-Specific Use Cases
Machinery:
Enhancing manufacturing processes to reduce defects and increase production efficiency. For instance, 6 Sigma can help identify and eliminate causes of machine breakdowns, improving overall equipment effectiveness (OEE).
Construction:
Streamlining project management and construction processes to minimize delays and cost overruns. By applying 6 Sigma, construction companies can improve project timelines and reduce waste.
Oil & Gas:
Reducing variability in production processes, ensuring consistent product quality and safety. 6 Sigma can be used to optimize drilling operations, reduce waste, and improve safety measures.
Automotive:
Enhancing production line efficiency and product quality through rigorous defect analysis. By implementing 6 Sigma, automotive manufacturers can reduce defects, improve quality, and increase customer satisfaction.
Maritime:
Optimizing maintenance schedules and reducing operational downtime through process improvement. 6 Sigma can help in ensuring the reliability and efficiency of maritime operations, from fleet management to crew training.
Challenges in 6 Sigma Implementation
Cultural Resistance:
Employees may resist changes to established processes. Overcoming this requires strong leadership and effective change management strategies.
Training Costs:
Significant investment in training and development. Implementing 6 Sigma often requires extensive training for employees at all levels.
Data Quality:
Inaccurate or incomplete data can hinder analysis and improvement efforts. Ensuring high-quality data collection and management is crucial for the success of 6 Sigma projects.
Addressing Challenges
Leadership Commitment:
Strong leadership support is essential to drive cultural change and ensure the success of 6 Sigma initiatives.
Ongoing Training:
Continuous education and training programs help build and maintain expertise in 6 Sigma methodologies.
Data Management:
Implementing robust data collection and management systems ensures that decisions are based on accurate and reliable data.
In overall, 6 Sigma stands as a robust methodology that revolutionizes how industries approach quality control and process improvement. Its data-driven and disciplined approach enables organizations to identify and eliminate defects, enhance efficiency and achieve higher customer satisfaction. By integrating 6 Sigma principles, companies across various sectors can obtain significant cost savings, improved product quality, and more streamlined operations.
6 Sigma principles can be implemented easily with robust Connected Worker Platform solutions, which provide the necessary tools for real-time data collection, process monitoring, and seamless collaboration across teams, thereby supporting the continuous improvement and data-driven decision-making that are central to 6 Sigma. As industries continue to evolve and face new challenges, the adaptability and effectiveness of 6 Sigma ensures its relevance and value in driving continuous improvement and operational excellence.
Learn more about VSight
See how VSight can help you with your field service, maintenance, onboarding and training operations.