What is Predictive Maintenance?
Predictive Maintenance is a proactive maintenance strategy that uses data analysis and monitoring technologies to predict when equipment or machinery is likely to fail, allowing maintenance to be performed just in time to prevent unexpected breakdowns. By leveraging real-time data from sensors, historical maintenance records, and advanced analytics, predictive maintenance helps identify potential issues before they lead to downtime, thereby optimizing equipment performance and extending its lifespan.
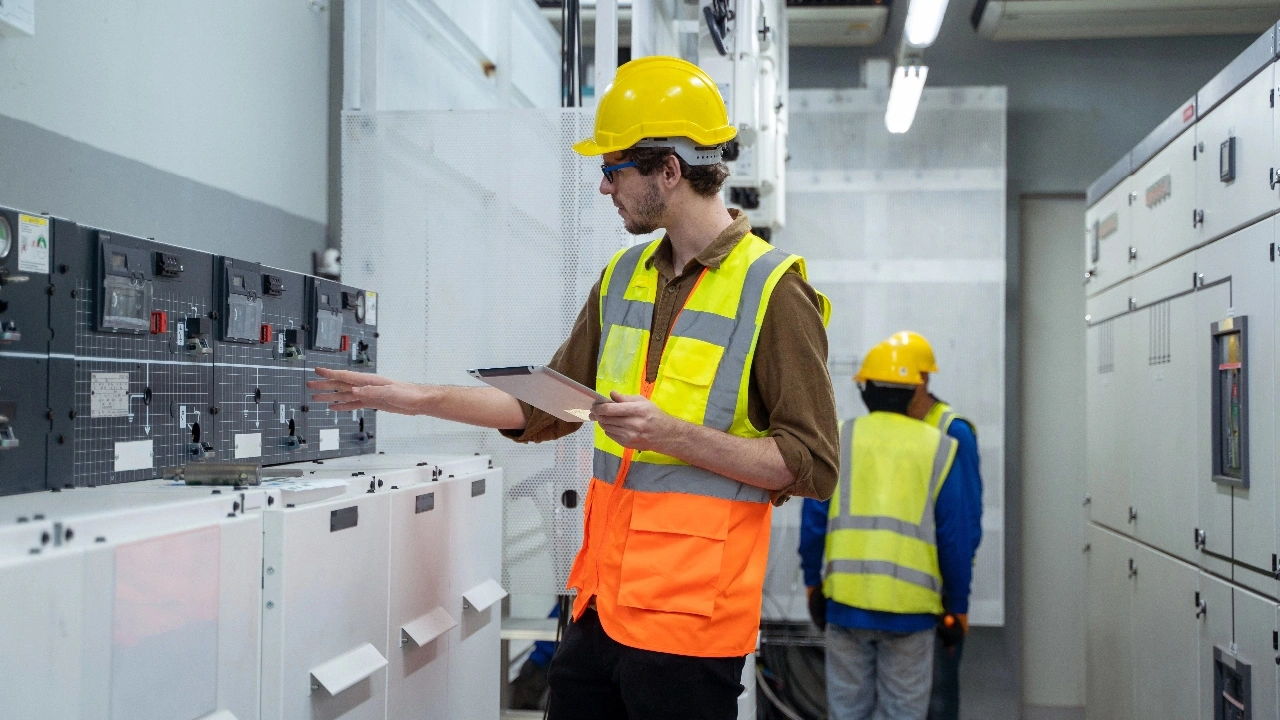
How Predictive Maintenance Works
Predictive maintenance involves continuous monitoring of equipment conditions using various sensors that track parameters such as vibration, temperature, pressure, and oil levels. The collected data is then analyzed using machine learning algorithms and predictive models to detect patterns and anomalies that indicate potential failures. Maintenance actions are scheduled based on the predicted health of the equipment, ensuring interventions are made only when necessary.
Benefits of Predictive Maintenance
Given the critical role of uptime and the detrimental effects of downtime, industries implement various strategies to optimize performance and operational efficiency.
Reduced Downtime:
By anticipating equipment failures, predictive maintenance minimizes unexpected breakdowns, leading to higher uptime and operational efficiency.
Cost Savings:
Timely maintenance interventions prevent extensive damage, reducing repair costs and extending the life of machinery.
Optimized Maintenance Schedules:
Maintenance is performed based on actual equipment condition rather than fixed intervals, improving resource allocation and reducing unnecessary maintenance activities.
Enhanced Safety:
Identifying potential failures early can prevent hazardous situations, ensuring a safer working environment.
Increased Productivity:
Reliable equipment performance leads to consistent production processes and improved productivity.
Applications in Various Industries
Machinery:
In manufacturing, predictive maintenance helps keep production lines running smoothly by preventing machine failures and optimizing maintenance schedules.
Oil & Gas:
Predictive maintenance is crucial for monitoring critical assets such as pumps, compressors, and pipelines, ensuring continuous operation and preventing costly shutdowns.
Mining:
By monitoring heavy machinery and equipment, predictive maintenance reduces the risk of breakdowns in harsh mining environments, ensuring efficient extraction processes.
Automotive:
Automotive manufacturers use predictive maintenance to maintain assembly lines and robotic systems, minimizing production interruptions and improving vehicle quality.
Construction:
Construction companies apply predictive maintenance to manage heavy equipment and machinery, preventing delays and maintaining project timelines.
Predictive maintenance represents a significant advancement in maintenance strategies, combining technology and data analytics to enhance the reliability, safety, and efficiency of industrial operations across various sectors. By implementing additional tools for remote collaboration and interactive work instructions next to predictive maintenance efforts, industries can achieve substantial improvements in operational performance and cost-effectiveness.
Learn more about VSight
See how VSight can help you with your field service, maintenance, onboarding and training operations.